Case Studies
Home // Case Studies
Case of Study A
Comparison with DCVG


CONTEXT
Major Oil & Gas company network in Belgium. Roads and railroads crossings.

access
12 measurement points, using existing Cathodic Protection Testing Stations (CPTS).

section
5400 m / 18000 ft section of buried pipelines in the countryside. Roads and villages crossing.

goal
Compare coating indications given by reflectometry (DRM) with those given by a surface method (DCVG)
results
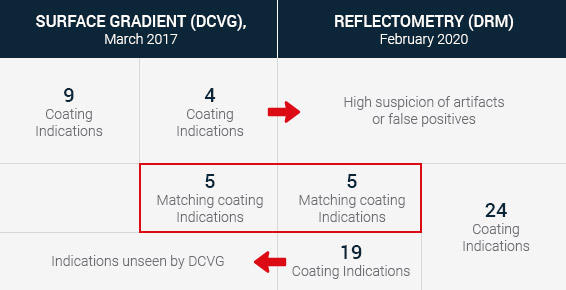
The reflectometry turned out to pick up much more indications than the surface gradient survey. Unless many of the detected defects developed between 2017 and 2020, this means that reflectometry has a more sensitive detection threshold than DCVG. 4 coating indications yield by DCVG are very large gradient picked up in immediate vicinity to roads, where the current distribution is affected, which makes the possibility of a false positive very likely.
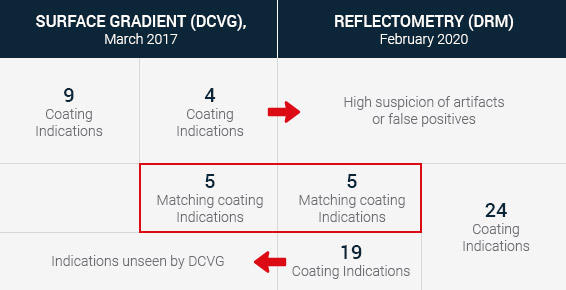
Case of Study B
Corrosion Costs Saved


CONTEXT
For a major US electrical utility company, in a big East coast city.

section
5000 feet of buried pipelines surveyed. All the section was under roads with a waterway crossing.

access
Through pre-existing access points, regular manholes.
results
6 most critical defects chosen to be excavated, successfully found with 15 feet excavation trenches, and repaired. What they would have done without this technology is dig up the entire 5000 feets.
Time and excavation costs saved (> 3 millions).